Products and services with innovative potential
• Procedure, installation and devices for measuring friction loss from transmission with parallel axes (chains, belts, connecting gears) according to medium speed, loading and characteristics of the lubricant
• Procedures and devices for measuring friction coefficients from mechanical friction torques, depending on the type of torque, medium speed, loading, with or without lubrication
• Modelling, simulation, optimization and experimental testing of road vehicle systems
• Range of antropomorphic grippers for industrial robots
• Procedure, installation and devices for measuring friction loss from transmission with parallel axes (chains, belts, connecting gears) according to medium speed, loading and characteristics of the lubricant
The procedure is based on measuring the global friction moment from a transmission, on separately measuring the friction moment from the transmission bearings, on the friction moment from the transmission resulted from the difference between the global moment and the bearings moment. A stand is equipped with a sensoring system for torque, tension force, temperature and pressure in lubrication circuits. The stand has a preset geometry for the separate testing of the bearings (with the help of some devices and in-house clutches). The correct evaluation of friction losses is part of the reduction process of energy loss from mechanical systems.
These were successfully applied in order to test more than 10 types of chains from 2013-2018.
• Procedures and devices for measuring friction coefficients from mechanical friction torques, depending on the type of torque, medium speed, loading, with or without lubrication
Research in this direction is based on a UMT tirbometer with four separate modules: a pin on disk module; reciprocating module, block on ring module; microscopes.
With the help of tools and in-house devices, friction coefficients can be measured for different types of friction torques with or without lubricant:
- device for measuring the friction coefficient from sleeve bearings. Friction coefficients have been determined, corresponding to specific functioning conditions: in an oscillatory rotation movement, with peripheral maximum speed of 0.2 m/s, contact forces within 10...300 N, drop lubrication;
- 4 device for measuring the friction coefficient, according to speed, contact force and temperature. The following friction coefficients have been determined, corresponding to specific functioning conditions: 1- oscillatory translatory motion, with a speed of 0...0,3 m/s, contact forces within 10...20 N, bath lubrication or without lubrication; 1- cicular translatory motion (on disk), with a speed of 0...7 m/s, contact forces within 10...20 N, bath lubrication or without lubrication.
• Modelling, simulation, optimization and experimental testing of road vehicle systems
Recent research has focused on suspension systems (passive suspension and active suspension, for steering and non-steering wheels, respectively), steering systems (including integral steering), windshield wiper systems, safety systems (e.g. seat belt tensioning systems). Research in these fields has materialized over the years in numerous articles published in ISI listed journals, IDB / ISI indexed journals and volumes, books published in national publishing houses, chapters in books published abroad, national research grants and contracts (including with beneficiaries from the automotive industry – e.g. Autoliv Romania), patents granted / proposals for patents, doctoral theses.
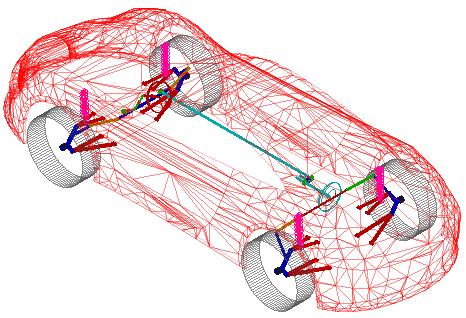

• Range of antropomorphic grippers for industrial robots
An important direction within the research followed the development of novel solutions of modular mechanical grippers, anthropomorphic, reconfigurable for industrial robots. Various versions have been developed: gripper with three fingers and two configurations; grippers with three fingers and four configurations; gripper with three fingers and a medium and continuous reconfiguration; gripper with four fingers and five configurations.
On beneficiary’s demand, sizes different from a human hand can be delivered: larger, up to 2.5 times the human hand or smaller, 0.25 from the dimension of a human hand.