Projects
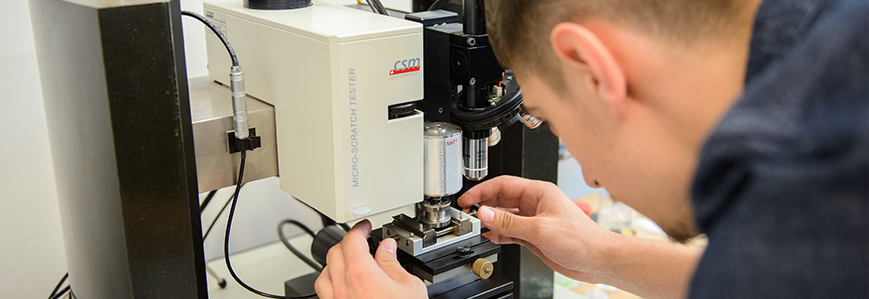
• Driving up Reliability and Efficiency of Additive Manufacturing (DREAM)
• Optimisation of the Ecotechnology of Induction Hardening of Large Diameter Bearing Rings
• Industrial Research Services Structure Surface Implant: Mechanical Features – DENTIX
• Driving up Reliability and Efficiency of Additive Manufacturing – Premiere H2020
• Driving up Reliability and Efficiency of Additive Manufacturing (DREAM)
The aim of the DREAM project is to significantly improve the performance of the alloying manufacturing process – PBF – to obtain titanium, aluminium and steel components concomitantly with the increase of their fatigue resistance and working duration. The objective of the project is to go beyond the present status of the laser-based technology by mastering every step of the processing chain. Among the various industrial applications of the PBF, the project is focused on components for prostheses, auto and casting in order to improve the proceedings for titanium, aluminium and steel.
Project Members
- Project Members
- Assoc. Prof. Dr. Eng. Munteanu Sorin
- Assoc. Prof. Dr. Eng. Bedő Tibor
- Lecturer Dr. Eng. Cristea Daniel
- Lecturer Dr. Eng. Gabor Camelia
- Scientific Researcher III Dr. Eng. Pop Mihai Alin
- Prof. Dr. Eng. Varga Béla
- Dr. Eng. Ghiuță Ioana
The project started on the 1st of October 2016 and spreads over a period of 36 months. It is an international HORIZON 2020 project, and Transilvania University of Brașov is a partner.
• Optimisation of the Ecotechnology of Induction Hardening of Large Diameter Bearing Rings
The general objective of the project is to optimize the technological parameters of the induction hardening of the bearing rings, specifically the decrease by about 30% of the refuse. The specific objectives are: to find the technological conditions that lead to defects; to rate the risk factors and to put up the reaction methodology; to implement the findings of the heating/cooling processes by new geometries of inductors which consider the new configurations. The desired outcome is to obtain a hardened layer on the active surface of the bearing ring which is uniform both in diameter as well as in section, having a pre-established thickness. The problems that appeared during the process, communicated by the economic agent to the project team from Transilvania University of Brașov are: the varying depth of the hardened layer on various areas from the ring circumference, the varying depth of the hardened layer reported to the profile section of the ring, fissures in the areas of maximum SHD (Surface Hardening Depth) or at the intersection of the rolling paths with small or large compartments.
Project Members
- Prof. Dr. Eng. Munteanu Daniel – project manager
- Assoc. Prof. Dr. Eng. Munteanu Sorin
- Lecturer Dr. Eng. Cristea Daniel
- Assoc. Prof. Dr. Eng. Bedő Tibor
- Lecturer Dr. Eng. Gabor Camelia
- Scientific Researcher III Dr. Eng. Pop Mihai Alin
- Prof. Dr. Eng. Miloșan Ioan
The financing instiution is The Executive Unit for Financing Higher Education, Research, Development and Innovation (Unitatea Executivă pentru Finanțarea Învățământului Superior, al Cercetării, Dezvoltării şi Inovării, CNCS-UEFISCDI). It is a BRIDGE project, having the duration of 24 months: from 30.09.2016 to 30.09.2018.
• Industrial Research Services Structure Surface Implant: Mechanical Features – DENTIX
The main objective of this project is to conduct researches on the structure of the surface of a dental implant. The research of the mechanical features of both the material and the proper implant has been undertaken. From the perspective of the mechanical resistance and the reaction with the adjoining tissues, titanium responds best to the requirements of the living organisms. Titanium can be used in stomatology both in pure state as well as an alloy. The pure titanium meets the necessary requirements of a dental implant. The most important of its properties is the fact that it is corrosion proof, due to the titanium dioxide pellicle that forms in contact with the environment, its thickness growing in direct proportion with the exposure duration. The continuous regeneration of this pellicle is what makes titanium corrosion resistant.
Project Members
- Assoc. Prof. Dr. Eng. Munteanu Sorin – project manager
- Prof. Dr. Eng. Crișan Aurel
- Prof. Dr. Eng. Varga Béla
- Prof. Dr. Eng. Geamăn Virgil
- Assoc. Prof. Dr. Eng. Bedő Tibor
- Lecturer Dr. Eng. Cristea Daniel
- Lecturer Dr. Eng. Gabor Camelia
- Scientific Researcher III Dr. Eng. Pop Mihai Alin
The project was won in public tender for research services organized by Dentix Millenium SRL.
• Driving up Reliability and Efficiency of Additive Manufacturing – Premiere H2020
The aim of the project is to study the effect of the direction of building by additive manufacturing on the anisotropy of components made of plastic materials with reference to a series of mechanic properties (hardness, elastic module, tear resistance, fatigue, and others). The properties of the components obtained by the process of additive manufacturing vary according to the type of manufacturing process, as there are many methods of 3D printing, each having advantages and disadvantages. Porosity favours the propagation of fissures, thus affecting the mechanical properties of the resulted components. For this reason, the main objective of the optimization of the additive manufacturing is to obtain density of over 99.5% for the components produced. The optimal functioning characteristics of the components largely depends on the direction of construction and the position in the working space, due to the fact that, as a rule, the powder present in the working space is considered partially used even if it is not sintered during the process.
Project Members
- Prof. Dr. Eng. Munteanu Daniel – project manager
- Assoc. Prof. Dr. Eng. Munteanu Sorin
- Lecturer Dr. Eng. Cristea Daniel
- Assoc. Prof. Dr. Eng. Bedő Tibor
- Lecturer Dr. Eng. Gabor Camelia
- Scientific Researcher Dr. III Eng. Pop Mihai Alin
The project unfolded between 2017 and 2019.
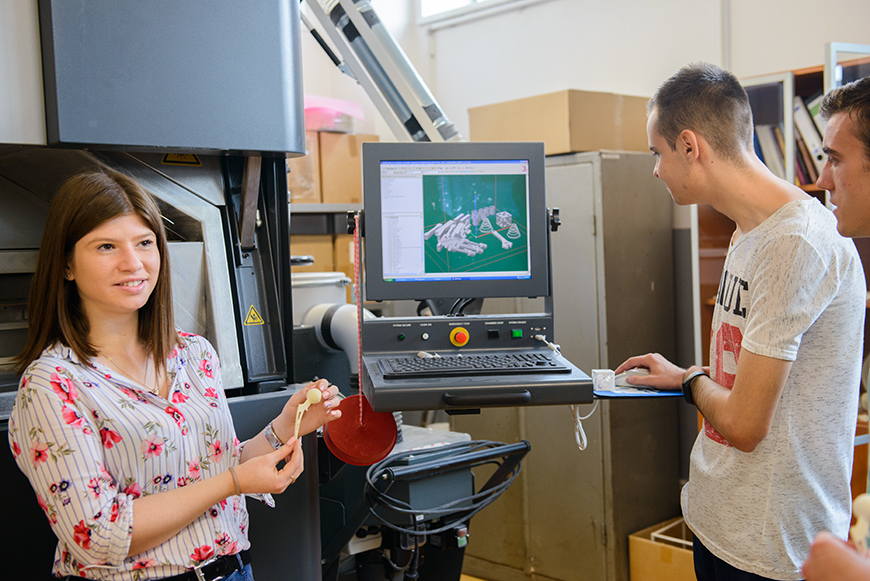