Infrastructure
• Induction melting furnace
• Nabertherm Furnace for thermic treatment
• Spectomaxx Spectrometer XF-BT
• Buehler Omnimet Image Analysis System
• FM 700 Micro Durometer
• L75PT/1400C Dilatometer
• Porosimeter Pascal 140
• DSC 200 F3 Maia/STA 449F3 Jupiter Thermal Analysis equipment
• WDW – 150 S Universal Testing Machine for metallic properties characterization
• Hydraulic Press
• CMS Instruments Micro Scratch Tester and Table Top Nanoindentation Tester
• CSM Instruments Calotest
• CSM Instruments Tribometer (pin-on-disk, ball-on-disk)
• Pulversette 7 Premium Line Planetary Mill
• Selective Laser Sintering 3D System SPRO 60 SD (SLS)
• Induction melting furnace
the maximum power of 20 kW, frequency of 15000Hz and a volume of the crucible of 1 – 1.2 dm3. It is equipped with a software that precisely controls the working power and the thermic regime prescribed for alloying.
In this furnace, in a pit stationary crucible (graphite or ceramic), ferrous, non-ferrous or special alloys (composite, special alloys, and others) can be produced.
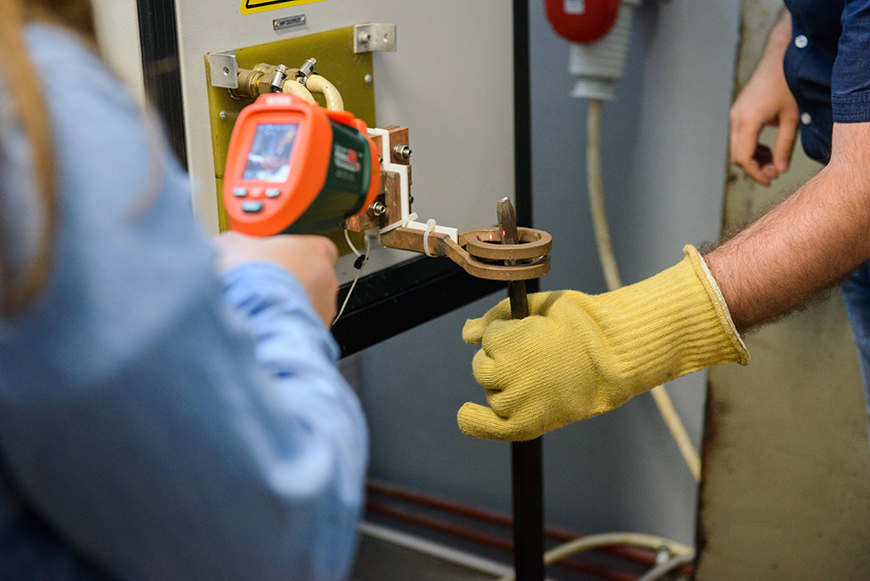
• Nabertherm Furnace for thermic treatment
furnace with electric resistor, having the working temperature of up to 1750⁰C and the possibility of programming the thermic treatment diagram (it has a memory for up to 8 simultaneous diagrams). The volume of the chamber/crucible is of 5 dm3. It allows for high precision thermic treatment ( 2oC), and it follows the diagrams for both metallic and non-ferrous matters for the complete temperature range (0-175oC). There is the possibility to control the working environment (argon, nitrogen, helium) by purification or adopting another specification of the furnace.
This equipment is able to perform thermic and special sintering treatments for both metallic and non-metallic (oxides) materials.
• Spectomaxx Spectrometer XF-BT
the precision of dosing the elements is up to hundreds percent and provides both qualitative and quantitative information.
It makes it possible, through the programs available, to perform chemical analysis for alloys including Fe, Al, Cu and Ti. The possibility to extend the programs for other alloys is included.
• Buehler Omnimet Image Analysis System
includes a Nikon microscope (having a resolution of up to 100x) and software for structural and quantitative analysis for the characterization of the metallic and non-metallic materials both from a quantitative and qualitative perspective.
Specific determinations for the grains dimension and form characterization, as well as the form and the quality of the inclusions can be determined.
• FM 700 Micro Durometer
performs the measurement of the HV hardness on micrometric surfaces (at structural level of grains), of metallic and non-metallic materials, for loads between 1–1000 gf. The Precidur software is designed for both manual and automatic operating mood, pre-established measurements and variation charts for hardness and distance.
• L75PT/1400C Dilatometer
developed for the study of phase transformation into solids for samples between 0.1 – 5mm and a maximum diameter of 6mm for the temperature range between 20oC and 1400oC, and the resolution 0.125 nm/digit. The software can determine the variation curves for dimension and temperature and the data processing to obtain information about the mechanism and kinetics of phase transformation.
• Porosimeter Pascal 140
allows for measurements of pores with volumes between 0.1 – 500 mm3, for samples of maximum 12x40 mm with a choice of pressures ranges between 0.1 – 400 kPa. The admitted porosity of the range of solid materials, metallic and non-metallic is up to 70%.
• DSC 200 F3 Maia/STA 449F3 Jupiter Thermal Analysis equipment
differential scanning calorimetry (DSC) and differential thermal analysis (DTA) are used in the area of thermal characterization of liquids and solids and can be used to analyse energetic effects such as: melting or crystallisation behaviour, solid-to-solid changes, polymorphism, purity analysis, specific heat determination. The determinations can be measured between 170oC and 600oC. The simultaneous thermal analysis (STA) refers to the simultaneous application of the thermal gravimeter (TG) and the differential calorimetry (DSC) on the same sample in the same chamber. The DCS analysis measures: the solidification, crystallisation and melting behaviour, crystallinity degree and thermal-kinetic analyse. The TG analysis determines: the volume modifications, the thermal stability for given temperatures, studies on corrosion, compositional analyses.
• WDW – 150 S Universal Testing Machine for metallic properties characterization
all the functioning parameters are controlled by the equipment’s software, which provides the testing bulletin in the variant chosen by the operator. The testing regime can be stationary or dynamic (including alternating fatigue testing). The testing force ranges between 1 and 150 kN.
The determinations are according to ISO standards and determinations of the mechanic properties can also be measured on non-standardized specimens, for a heat range between 1500C and 12000C.
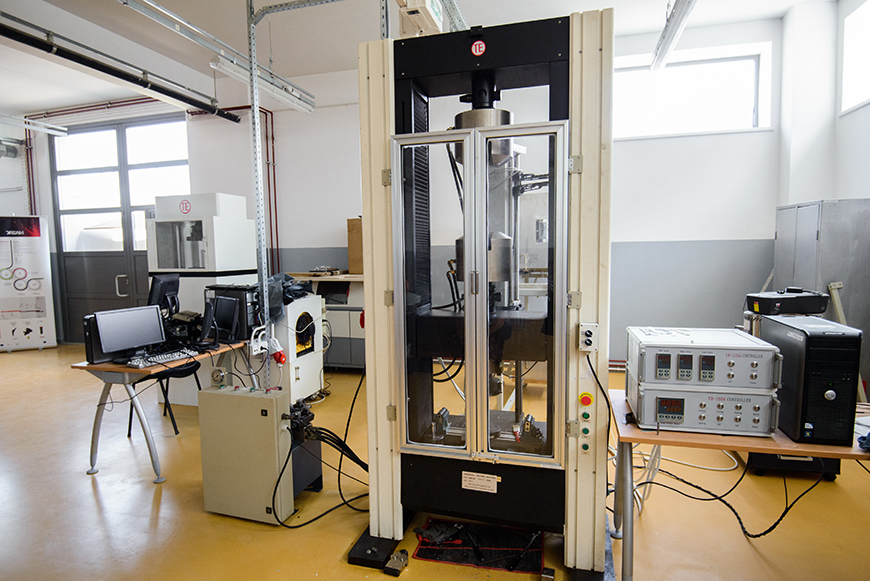
• Hydraulic Press
the maximum applied force is of 2500kN, and the working area is of 300 x 300 x 490 mm.
It performs plastic deformation of metallic materials, compression and pressing extrusion of powders, etc.
• CMS Instruments Micro Scratch Tester and Table Top Nanoindentation Tester
the nano indentation head is utilised for determining the mechanic behaviour of surfaces by indentation at depths of nano-micro scales. The maximum load is 500nM, and the maximum load applied to the indenter is under 0.05nM. The micro scratch head is used to establish the adherence of the coatings, the shallow layer on the layer below.
This nano-indenter can be used for the characterization of the hard or soft materials and coatings, both organic and inorganic one. It can also measure the elasticity module and hardness.
• CSM Instruments Calotest
is used to analyse the coatings with thickness varying between 0.1 and 50 µm. The typical coatings that it can analyse include CVD, PVD, plasma spray coatings, anodic oxidation layers, surfaces treated by ion sputtering or ion plating, chemical and galvanic deposits, polymers, paints, and lacquers.
• CSM Instruments Tribometer (pin-on-disk, ball-on-disk)
is used to determine friction and wear behaviour of the solids and coatings, including the possibility to modify the period of analysis, the contact load and the rotation speed. The maximum rotation speed can be of 500 rot/min and the maximum load of 10N.
• Pulversette 7 Premium Line Planetary Mill
grinds the materials up to nanometre dimensions. The automatic control of the grinding process guarantees that pre-established quality parameters are met.
• Selective Laser Sintering 3D System SPRO 60 SD (SLS)
the installation assists the manufacturing of products made of ceramic, metallic and polymeric or composite powders, regardless of their geometrical complexity. The sintering furnace attached to the SLS installation sinters the ceramic and metallic powders, and according to the desired specifications, their infiltration with different metals. The maximum dimensions for the specimen can be 315x315x415mm, and the files must have the extension .stl in order to be accepted.